Aluminum Alloy Heat Treatment
Updated: 14 Mar 2024
Heat treatment of aluminum alloys, 4 types, what problems will be encountered
Annealing, quenching, aging, regression treatment, do you clearly distinguish between these heat treatments? The function of heat treatment is to improve the material's mechanical properties, eliminate residual stress and improve the machinability of aluminum alloys. Heat treatment processes can be divided into two categories: preliminary heat treatment and final heat treatment, depending on the purpose of the treatment.Purpose of preliminary heat treatment is to improve processing performance, eliminate internal stress and prepare a good metallographic structure for final heat treatment. Its heat treatment processes include annealing, quenching, aging, regression treatment, etc.
Final heat treatment aims to improve mechanical properties such as hardness, wear resistance and strength.
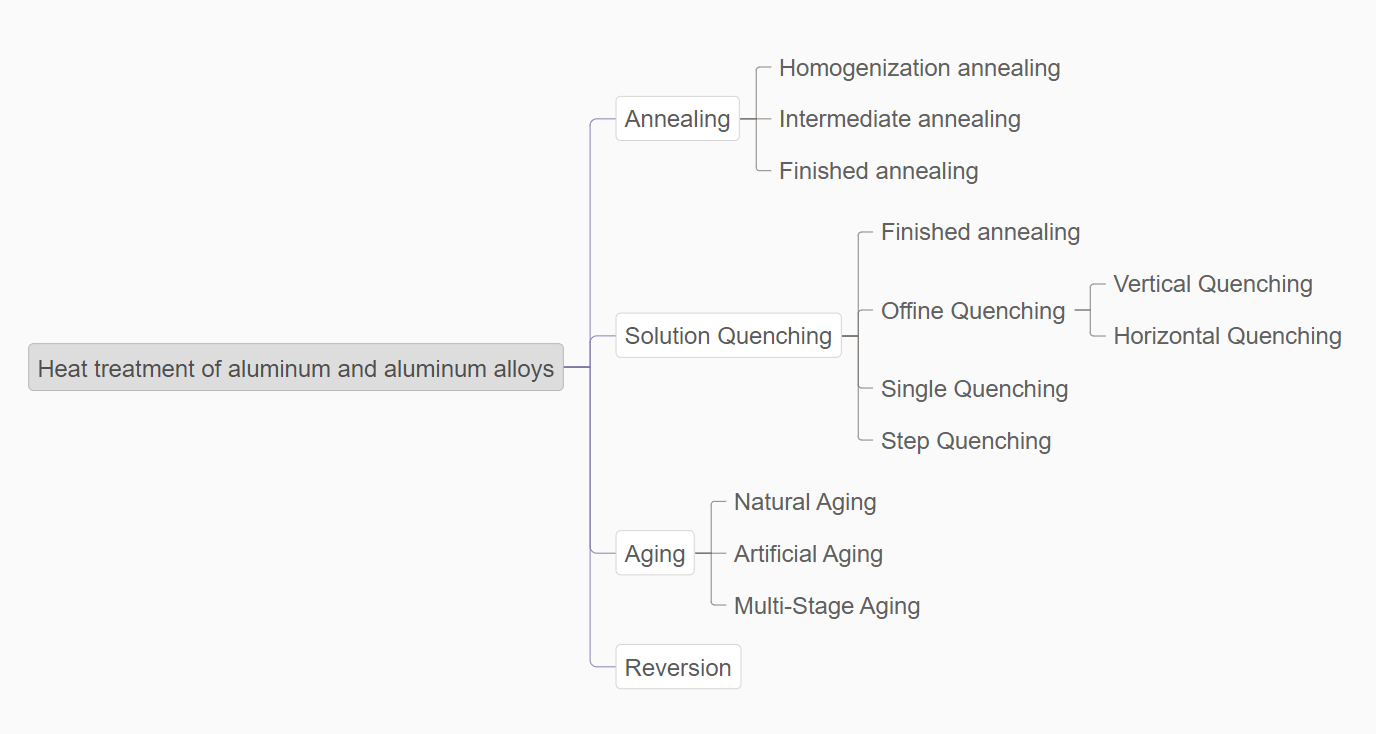
Basic principles of heat treatment of aluminum and aluminum alloys
1. AnnealingThe product is heated to a specific temperature, kept warm for a certain period, and then cooled to room temperature at a specific cooling rate. Through atomic diffusion and migration, the structure is made more uniform and stable, and internal stress is eliminated, which can greatly improve the plasticity of the material, but the strength will be reduced.
Ingot homogenization annealing: long-term heat preservation at high temperature, and then cooling at a certain speed (high, medium, low, slow) to homogenize the chemical composition, structure and properties of the ingot, which can increase the material plasticity by about 20% and reduce extrusion The force is about 20%, the extrusion speed is increased by about 15%, and the surface treatment quality of the material is improved at the same time.
Intermediate annealing: also known as local annealing or inter-process annealing, is to improve the plasticity of the material, eliminate the internal processing stress of the material, and maintain it at a lower temperature for a shorter time to facilitate continued processing or obtain a specific combination of properties.
Complete annealing: Also known as finished product annealing, it is maintained at a higher temperature for a certain period to obtain a softened structure in a completely recrystallized state with the best plasticity and lower strength.
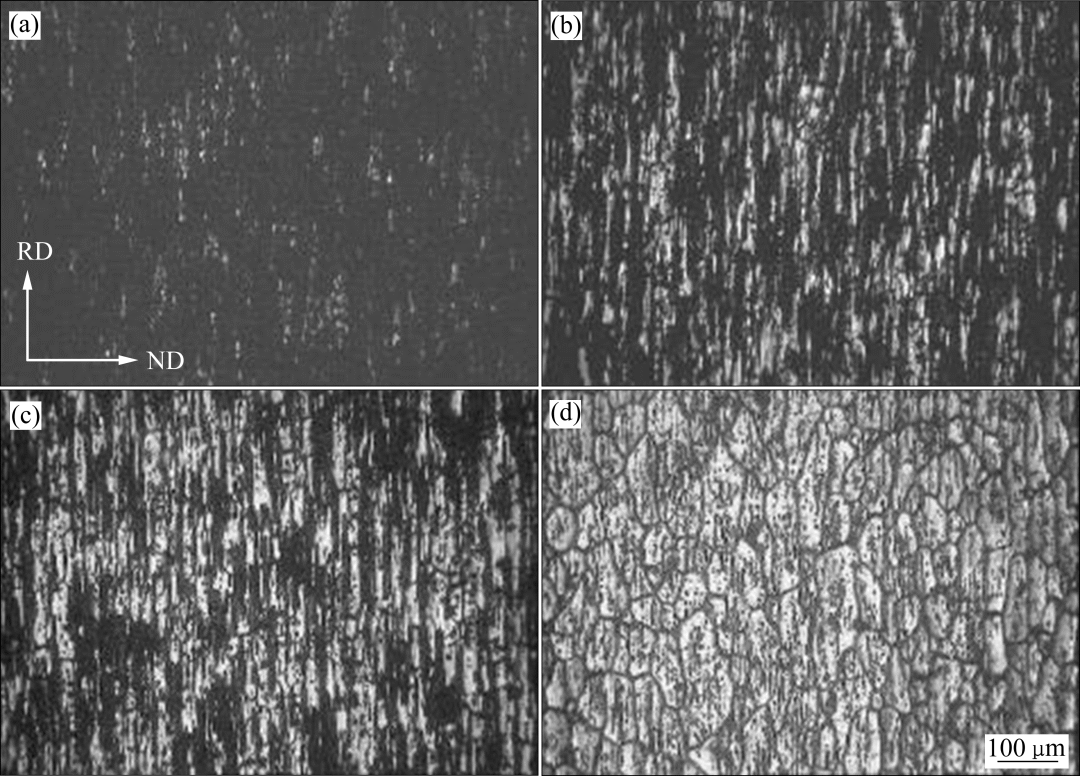
The aluminum alloy material that can be strengthened by heat treatment is heated to a higher temperature and maintained for a specific time so that the second phase or other soluble components in the material are fully dissolved into the aluminum matrix to form a supersaturated solid solution, and then quickly cooled When this supersaturated solid solution is kept at room temperature; it is an unstable state. Solute atoms may precipitate anytime because they are in a high-energy state. However, the material has high plasticity at this time and can be cold-worked or straightened.
Online quenching: For some alloy materials with low quenching sensitivity, the high temperature during extrusion can be used for a solid solution and then quenched with air cooling (T5) or water mist cooling (T6) to obtain a specific structure and performance.
Offline quenching: For some alloy materials with high quenching sensitivity, they must be reheated to a higher temperature in a special heat treatment furnace and kept for a certain period, and then quenched into water or oil with a transfer time of no more than 15 seconds to obtain a particular According to different equipment, it can be divided into salt bath quenching, air quenching, vertical quenching and horizontal quenching.
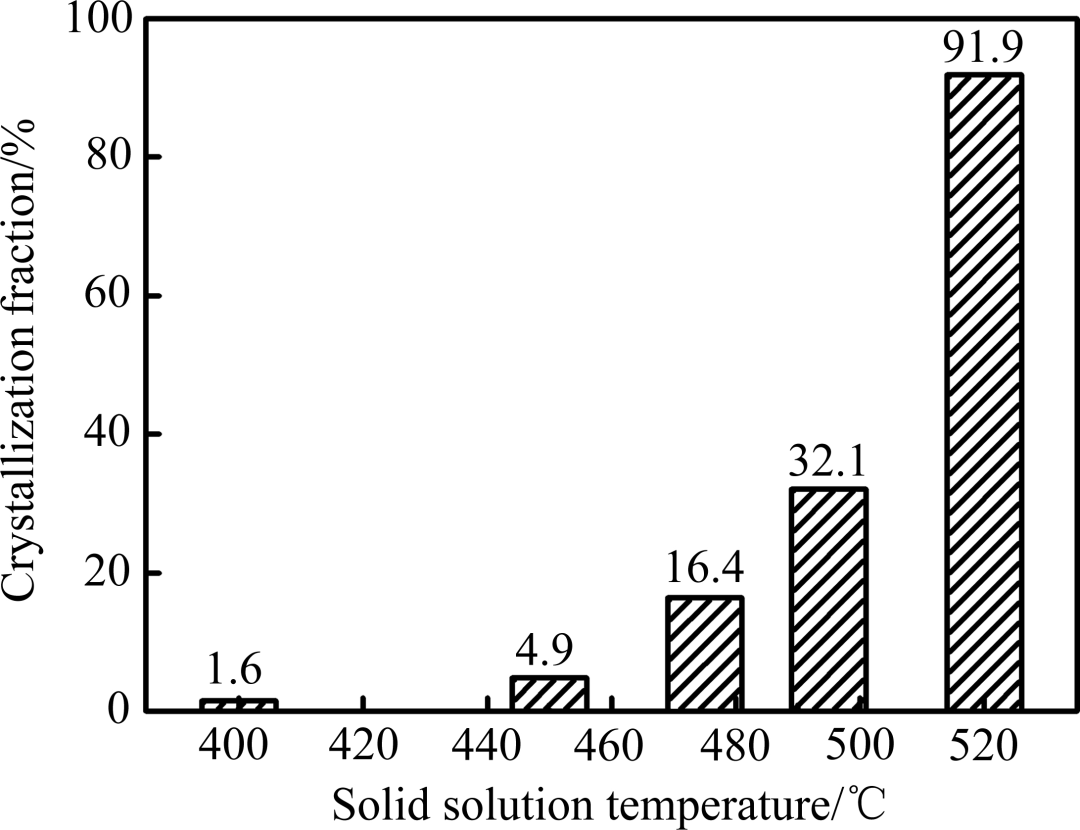
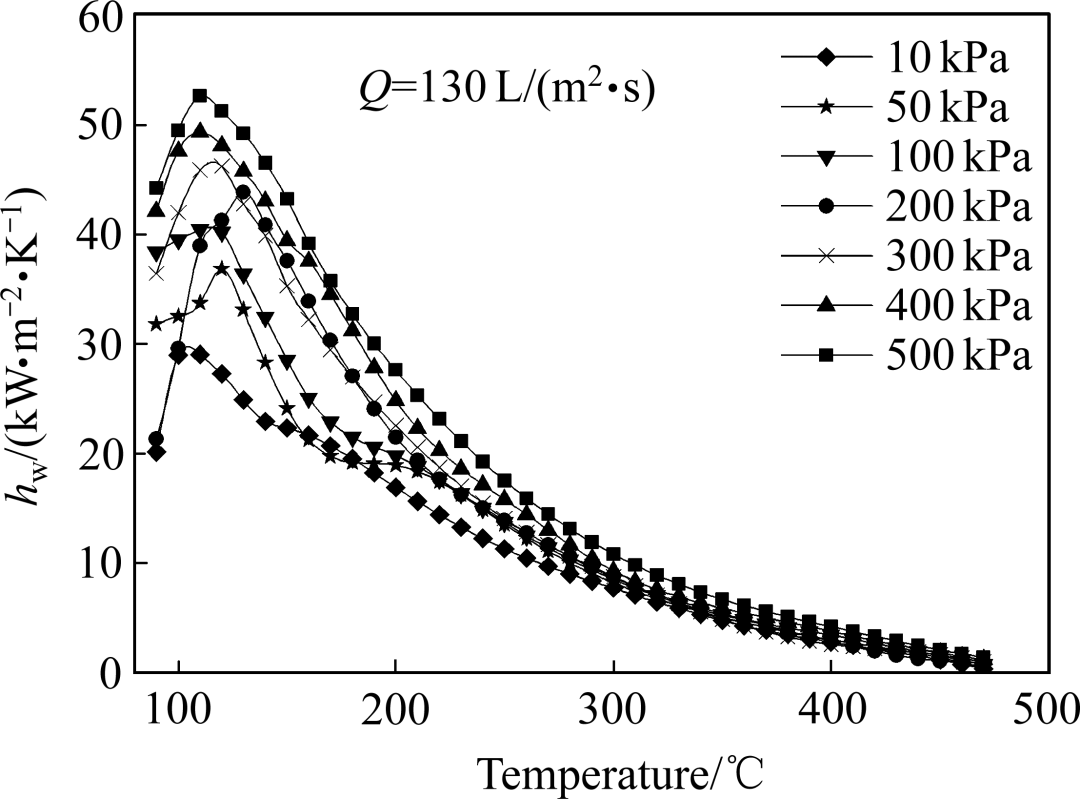
After solid solution quenching, the unstable supersaturated solid solution will decompose if the material is kept at room temperature or higher temperature for some time. The second phase particles will precipitate (or precipitate) from the supersaturated solid solution and be distributed in α (AL ) around the aluminum grains, resulting in a strengthening effect called precipitation (precipitation) strengthening.
Natural aging: Some alloys (such as 2024, etc.) can produce precipitation-strengthening effects at room temperature, called natural aging.
Artificial aging: Some alloys (such as 7075, etc.) have little evident precipitation strengthening at room temperature, but the precipitation strengthening effect is obvious at higher temperatures, called artificial aging.
(Artificial aging can be divided into under-aging and over-aging:
Under-aging: To obtain specific properties, control a lower aging temperature and maintain a short aging time.
Over-aging: To obtain certain special properties and better comprehensive properties, aging is carried out at a higher temperature or under a longer heat preservation time. )
Multi-level aging: The aging process is divided into several stages to obtain specific special properties and good overall performance. Can be divided into two-stage and three-stage aging
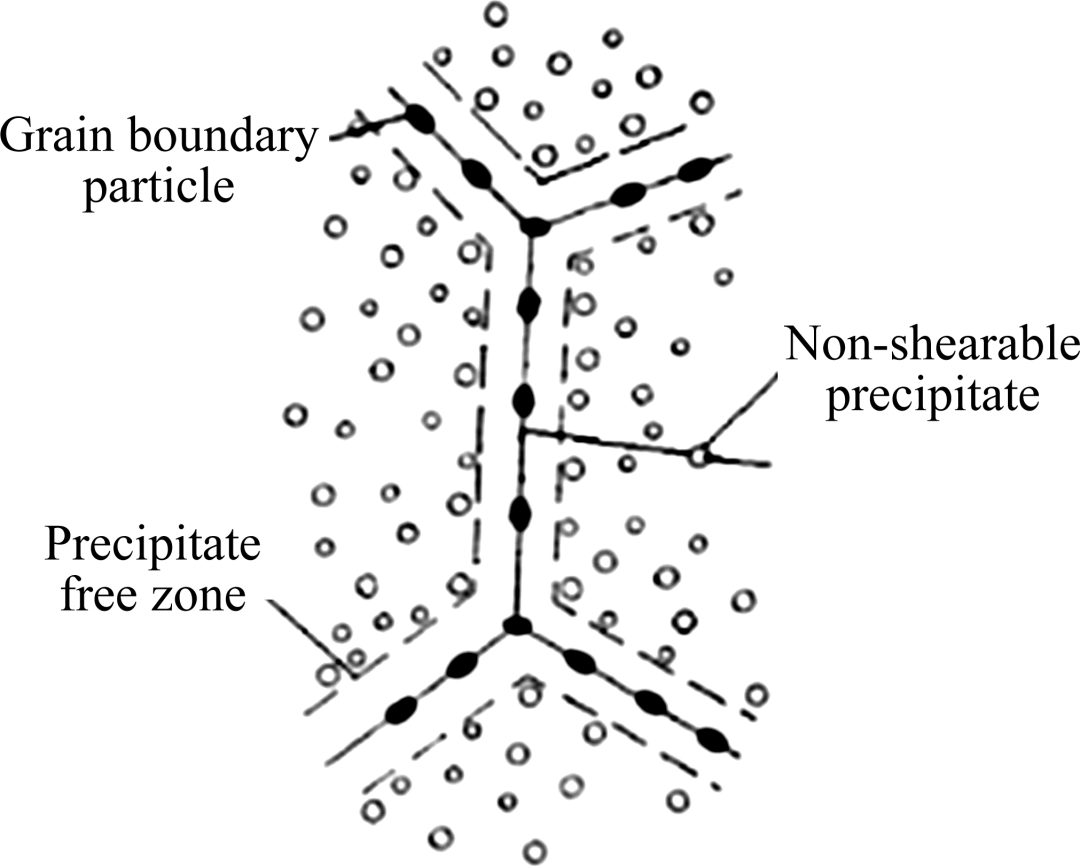
To improve the plasticity and facilitate cold bending or correction of shape tolerances, the quenched and aged products can be restored to the new quenched state by heating them at high temperatures for a short period, which is called regression treatment.
For the heat treatment of aluminum, the most reported issues include:
1. Heating/heating up too quicklyThis can cause thermal deformation and should be prevented. Proper placement of components helps distribute heat evenly.
2. Residual stress levels are higher than expected
Heat treatment changes mechanical properties and directly affects residual stress levels. The following are possible reasons: during quenching (including when the casting is cooled after solidification), the cooling rate on the surface and inside is quite different; the heating rate is inappropriate; temperature changes occur in intermediate steps; etc. Residual stresses are related to factors such as (large) differences in cooling rates, the cross-sectional thickness of the component, sudden changes in cross-sectional dimensions and the strength of the material. It is important to remember that the stresses caused by quenching are much greater than those caused by other processes, including casting.
3. Time/temperature/quenching parameters fluctuate
They will lead to deviations in mechanical or physical properties from part to part and from batch to batch. Causes include part transfer times that are too long, improper quenching (too slow), overheating, underheating, or changes in time-temperature parameters during precipitation hardening. For example, if the time is too long and the temperature is too high, larger particles (precipitates) will precipitate.
4. Overheating
At this time, incipient or eutectic melting will likely occur. For example, solution heat treatment temperatures are close to the melting points of many aluminum alloys (especially the 2xxx series, which are often only a few degrees below their melting points). An appropriate temperature is required to promote the dissolution of solid alloy elements.
5. Insufficient heating
This results in a loss of mechanical properties due to insufficient supersaturation. If the aging temperature is too low or the aging time is too short, it is not easy to form a solute atom accumulation zone (GP zone), resulting in low strength after aging.
6. Insufficient quenching causes deformation
The problem/difficulty with this is the action of the part entering the quenching agent, especially if manual quenching is necessary. The component must enter the quenching agent smoothly. (In heat treater jargon, avoid letting the part "slap" the quenchant.) Even heat transfer throughout the part prevents differential cooling and strain. Changes in heat transfer in the horizontal direction are generally more detrimental than changes in the vertical direction. It is very important to maintain the quenching agent at the appropriate temperature, control its temperature rise, ensure its uniform flow, select the most appropriate quenching agent (such as air, water or polymer), etc. For example, according to the needs of a specific application, the cooling rate of the polymer can be adjusted by changing the concentration, temperature and stirring intensity to ensure uniform heat transfer and quenching speed during the nucleate boiling stage. Quenching agent maintenance is also important for components with complex shapes, such as forgings, castings, impact extrusions and components made from thin sheets, lower quenching rates can be used to improve the deformation behavior.
7. Surface peeling/high-temperature oxidation
The heat treatment problem diagnosis column "High Temperature Oxidation – Case Study" in the February 2016 edition of "Industrial Heating" discusses this issue in detail.
8. Excessive aging
This may cause loss of mechanical properties. If the aging temperature is too high or the aging time is too long, the critical nucleation size of the precipitated phase in the supersaturated solid solution will increase, causing the strength index to decrease after aging.
9. Insufficient timeliness
This may also result in loss of mechanical properties.
10. Improper natural aging
The natural aging time varies, about 5 days for 2xxx series alloys and about 30 days for other alloys. The 6xxx and 7xxx series are less stable at room temperature and changes in mechanical properties will persist for many years. In some alloys, natural aging is inhibited or delayed several days after being treated at low temperatures of -18°C (-1˚F) or below. It is common practice to complete forming, straightening and stamping before the material properties are changed by aging. For example, low-temperature treatment is often used for 2014-T4 rivets to maintain good riveting performance.
11. Improper artificial aging
Artificial aging (precipitation heat treatment) is a longer, lower-temperature process. Temperature control is critical and temperature uniformity of ±6˚C (±10˚F) must be strictly maintained. The optimal target for temperature uniformity should be ±4˚C (±7˚F).
12. Insufficient heat preservation time
The consequence is that the desired mechanical properties still need to be achieved. A time that is too short will result in insufficient supersaturation, while a time that is too long will easily cause deformation of the component.
13. Poor temperature uniformity
This can lead to unachievable or even altered mechanical properties. Typical requirements for process temperature uniformity are ±6˚C (±10˚F), while most aerospace applications desire ±3˚C (±5˚F).
14. Improper cold processing after solution treatment
This is often due to a need for more understanding of how the alloy being treated will react. For example, cold working of quenched 2xxx series alloys will significantly increase its reaction to subsequent precipitation treatments.
15. The cooling speed is not enough during the annealing of solution heat-treated products
The maximum cooling rate must be maintained at 20˚C (40˚F) per hour until the temperature drops to 290˚C (555˚F). The cooling rate below this temperature is less important.
16. Improper placement of components
This can lead to component distortion, mainly because the quenching agent cannot transfer heat fast enough to achieve the desired mechanical properties. Improper placement may also cause thermal deformation (because the creep strength of aluminum is not strong enough).
Aluminum alloy heat treatment is a complex process, but Shenghai Aluminum, a professional aluminum profile manufacturer, is very mature in these processes. Of course, heat treatment is determined based on product application and process. If your product requires this heat treatment, please contact us. We have professional engineers to assist in completing your aluminum profile project.